At the ceiling …instead of metal ….we’ll use wooden beams to avoid dew point. On this video I just show where the metal parts will come. Far away from the facade. We can prepare them at this stage.
Before pouring concrete we can take 1 of metal beams on each side and rope it to the facades. This way is way easier to get the facades in a perfect position (while the concrete sets). After concrete sets we can take them down. We’ll put them in their final position like a day later.
On the lower part we don’t bother that much with dew point (as mentioned before). The interior temperature is quite constant. The earth’s temperature under the house is relatively constant as well.
Foundations poured !
One of my favorite part of the construction. The niche / holes for the concrete are the form as well. After we are ready with digging the holes, we can setup the frame quite fast. So concrete can follow. I might risk to say that could be a 1 day job.
No need for plywood frames and extra workmanship. None of building, transporting forms for weeks. It can be done in one day. The next morning concrete set enough for the lightweight wooden beams. We can start to build the roof. Yes that crazy as it might sound.
Till night we’ll have the whole framework of the roof. In case we have quite a few persons on site. If there are just 2-3 persons on site it might take a bit longer. Anyways it leaves any construction method in the dust.
The building is water proofed from above at this stage. We won’t put the electric cables, insulation and ceiling at this point. We can postpone it for later.
The upper membrane (roof) is easy to take down. (or slide it afar). It takes minutes. Even on a rainy day you can work on an opened roof. It takes a few minutes … to “open” and close sections.
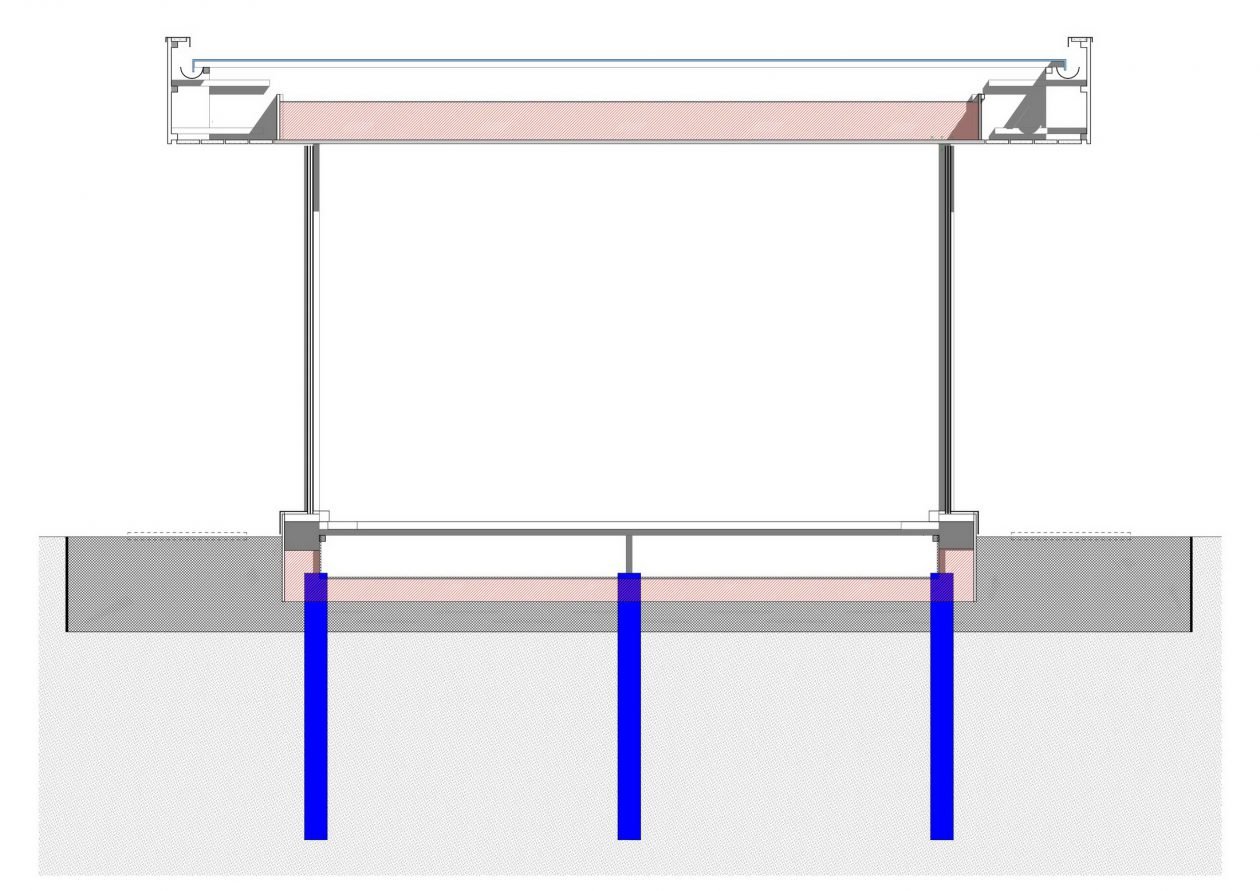
Under the house we’ll fill it up with gravel. Water will drain away quite easily. Note the water draining pipes at the edges of the section. (The red will be the insulation in later stages.) The gravel is below that.
Quite funny. The only cost regarded to foundations is concrete itself. That’s relatively cheap. Ana additional cost would be digging the holes with a rotating screw. Piling. That might be a screw attached to a bobcat … or a similar machinery. Depends on deepness, soil and climate. Your local engineer and geo expert will decide here.
What method is cheaper, faster, better in your area.
The odds are this particular design (engineering solution) can be built on almost any other soil. Even wetland. Piling. Where others would need to pay fortunes to build. The house is lightweight, strong an d flexible. It can be built literally anywhere.
The worst building terrains wouldn’t be a problem in our case. On the contrary… It would be full of nature and none of curious neighbors. Meanwhile it’s the cheapest to buy. In similar places a big piling machine would get stuck. But not a small one (that we need).
In case you buy the pre mixed concrete-sand variant …. you won’t need to bring a truck on site bringing concrete. You’ll use it from pre mixed bags. You will have time to pour it slowly. The consistency would be perfect. Evan better maybe that that from the truck. Easier to bring it on difficult terrains. This method (used as an extension) won’t destroy existing gardens with the perfect lawn.
Again : I would choose the already pre mixed concrete sold in bags. It just needs water. Slowly and patiently filling up the holes. It might take a few hours more but it worth it.
Adding some chemicals to the water / concrete for water insulation would be a great idea. It would protect the metal. It depends on climate soil. Your local certified engineer should decide what’s best in your case. Or does it worth the extra cost. What’s right for you and for your budget.
Do you need extra “paint” on the metal or some water proofing chemicals within the concrete. Maybe both. I would go with both. Why not. Compared to the overall budget they are not that expensive. Gained longevity might worth it. Depends on case by case. .